PSA Nitrogen Generators
(by Newttorr Pumps and Systems Pvt. Ltd.)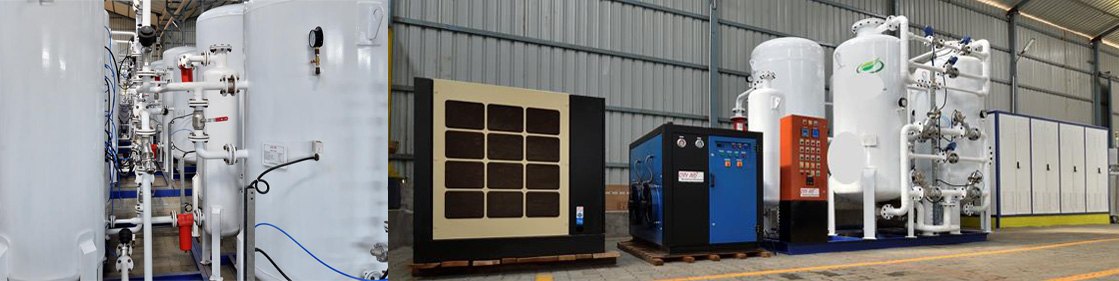
Welcome to Newttorr Pumps and Systems Pvt Ltd, your premier destination for state-of-the-art PSA Nitrogen Generators. Our innovative solutions are designed to meet the high demands of modern industries, providing reliable, efficient, and cost-effective nitrogen generation on-site. Explore how our PSA Nitrogen Generators can revolutionize your operations, ensuring a continuous supply of high-purity nitrogen whenever you need it.
The company under the able stewardship of Mr.K L Girdhar, [Alumni IIT Delhi, Chemical Technology (1975 batch)] who has executed the following projects in: Design, engineering, supply, and commissioning of various adsorbent-based gas plants, including PSA nitrogen and gas plants.
Our expertise extends to gas purification systems, such as biogas, de-oxo, gas separations, and drying units. Additionally, we provide ammonia cracking units, ammonia handling and storage systems, and a variety of piping projects.
Enquiry Form
